Unlock the secrets of effective facility maintenance planning with this comprehensive guide. Discover proven strategies, industry best practices, and valuable insights to optimize your maintenance operations and enhance your facility's performance.
Understanding Facility Maintenance Planning
Imagine your facility running like a well-oiled machine. Â Equipment operates flawlessly, spaces are clean and welcoming, and unexpected breakdowns are a thing of the past. This is the result of effective facility maintenance planning.
Facility maintenance planning goes beyond simply fixing things when they break. It's a proactive strategy for keeping your building and assets in top condition, extending their lifespan, and saving you time, money, and unnecessary stress.
Consider it preventative care for your building. Instead of waiting for a major issue to arise, you take steps to prevent it altogether. Regular inspections, planned maintenance, and timely repairs all contribute to a well-functioning facility.
Why is this so important? Here's a breakdown:
Whether you manage a bustling restaurant, a busy office, or a factory, a solid facility maintenance plan is essential for success. It's about being proactive, strategic, and ensuring your facility operates at its best, every single day.
Key Components of a Maintenance Plan
A well-structured facility maintenance plan is a blueprint for success, ensuring your building operates efficiently. Here are the key components:
1. Â Asset Inventory: Â Begin by creating a comprehensive list of all equipment, systems, and assets within your facility. This includes everything from HVAC units and electrical systems to elevators and fire safety equipment. Â
2. Â Preventive Maintenance: This is the foundation of any effective plan. Establish a schedule for routine inspections, cleaning, and servicing of all assets. The frequency depends on the asset's usage and manufacturer recommendations. For instance, a busy restaurant might schedule daily cleaning and weekly filter changes for its HVAC system.
3. Reactive Maintenance: While preventive measures are ideal, unexpected breakdowns can still happen. Having a system for handling these situations is crucial. Â This includes outlining procedures for reporting issues, contacting vendors, and managing emergency repairs.
4. Â Predictive Maintenance: Take your maintenance plan further by incorporating predictive techniques. This involves using data and technology, like sensors and analytics, to anticipate potential failures before they occur. By identifying issues early, you can often avoid costly downtime and major repairs.
5. Â Budgeting and Tracking: Facility maintenance planning requires financial planning. Â Allocate budget for routine maintenance, emergency repairs, and potential equipment replacements. Â Regularly track expenses to ensure you stay within budget and identify areas for potential savings.
Creating a Maintenance Schedule
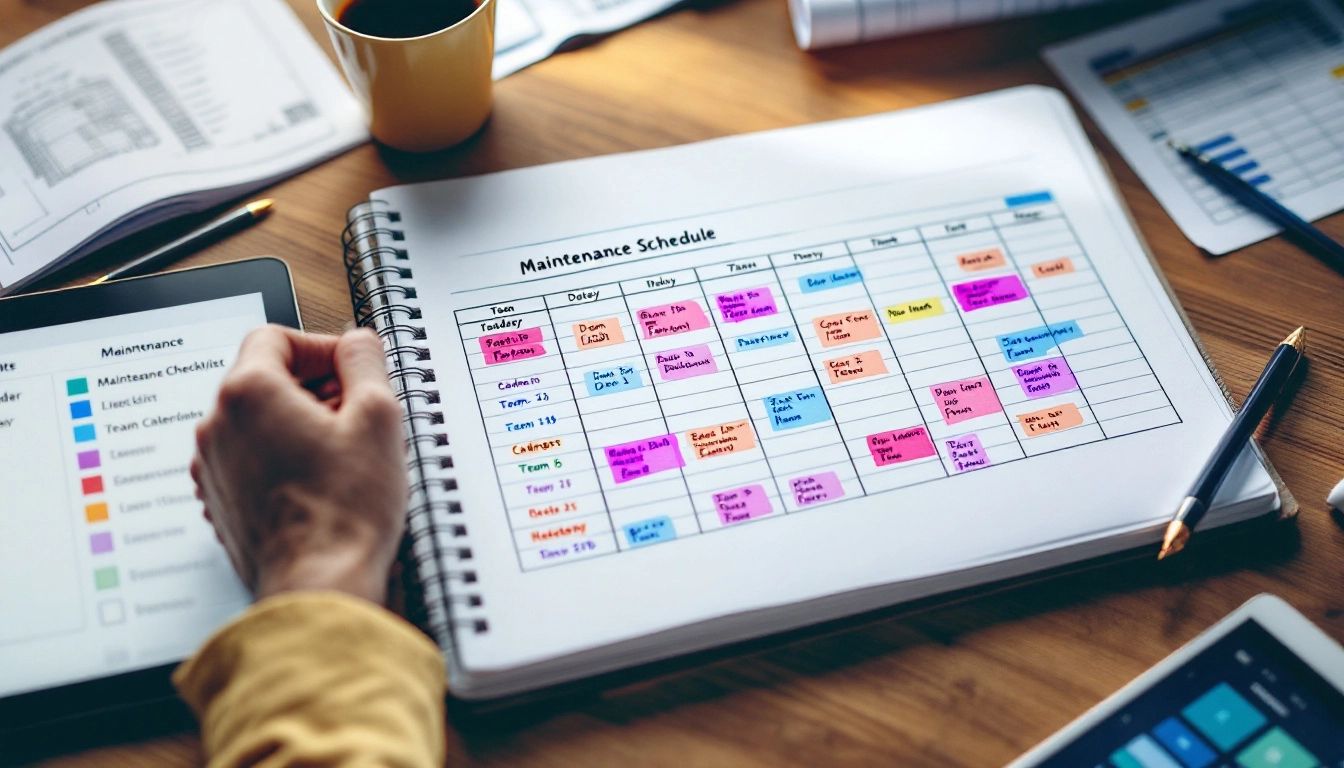
Now that you understand the core elements of facility maintenance planning, let's focus on creating a workable schedule. This is where your plan turns into a practical roadmap.
1. Prioritize Your Assets: Not all assets are equal. Some, like your HVAC system or fire suppression system, are mission-critical. Others, like a secondary office printer, are less vital. Rank your assets based on their importance to daily operations and the potential impact if they fail.
2. Â Consult Manufacturer Recommendations: This is your starting point for determining maintenance frequency. Manufacturer manuals often outline recommended inspection and service intervals. For example, a commercial refrigerator might require monthly coil cleaning and an annual compressor check.
3. Â Factor in Usage and Environment: Adjust the manufacturer's recommendations based on the asset's usage and operating environment. A delivery truck covering many miles in a dusty warehouse will need more frequent maintenance than a lightly used vehicle in a climate-controlled facility.
4. Â Establish a System: Use a calendar, spreadsheet, or specialized facility maintenance software to create your schedule. Clearly outline:
5. Â Don't Forget Reactive Maintenance: While your schedule focuses on prevention, incorporate a system for handling unexpected issues. This includes designating personnel responsible for handling emergency repairs and having a clear process for reporting and addressing problems.
6. Â Review and Adapt: Your maintenance schedule isn't set in stone. Regularly review it, especially after equipment failures or changes in facility usage. Analyze data on breakdowns, repair costs, and downtime to identify trends and adjust your schedule for optimal effectiveness.
Remember, a well-crafted facility maintenance plan is a dynamic tool that adapts to your building's needs. By taking a proactive, organized approach to maintenance, you set your facility up for long-term success and significant cost savings.
Technology in Facility Maintenance
Gone are the days of clunky spreadsheets and overflowing filing cabinets. Facility maintenance planning has gone digital! Â Modern technology offers a game-changer for managing your building's needs, making it simpler and far more efficient. Â
Software platforms designed for facility maintenance are becoming increasingly popular. Â These platforms can:
For example, ResQ helps restaurants manage their repair and maintenance operations – from asset tracking to vendor management – saving them time and money.
By embracing technology, you're not just modernizing your facility maintenance planning; you're setting the stage for smoother, more cost-effective operations overall.
Implementing and Monitoring the Plan
You've invested time and effort into crafting a facility maintenance plan – now it's time to put it into action! Effective implementation is all about communication, organization, and adaptability.
Clear Communication is Key: Ensure everyone on your team, from maintenance technicians to department heads, understands their roles and responsibilities within the plan. Â Regularly communicate schedule updates, procedural changes, and any relevant information.
Use Technology: Ditch those cumbersome spreadsheets and embrace facility maintenance software! Platforms like ResQ can streamline your entire operation, centralizing asset information, automating reminders, and simplifying communication. Â
Track Everything: Meticulous record-keeping is crucial.  Log all maintenance activities – both preventive and reactive – including dates, tasks, parts used, costs, and any observations. This data is invaluable for monitoring your plan's effectiveness and identifying areas for improvement.
Analyze and Adapt: Regularly review the data you've collected. Â Are you experiencing fewer equipment breakdowns? Â Are you staying within budget? Â Are there any recurring issues that need addressing? Â Use this information to fine-tune your plan, adjust maintenance schedules, and optimize your facility's performance.
Remember, facility maintenance planning isn't a "set it and forget it" task. It's about continuously evaluating, refining, and adapting your approach to ensure your building operates at peak efficiency and remains a safe, productive environment.
Continuous Improvement in Maintenance Planning
Even with a meticulous plan, facility maintenance planning is an ongoing journey.  The world of facilities is always evolving – equipment ages, technologies advance, and your building’s usage patterns change. To stay ahead, you need a commitment to continuous improvement.
Think of your plan as a living document that requires regular checkups and adjustments. Here's how to ensure your facility maintenance planning continues to deliver:
1. Â Data is Your Friend: Â Regularly analyze the data you've collected on repairs, costs, and equipment downtime. Look for patterns and trends. Â Are certain assets breaking down more frequently than expected? Â Are there seasonal spikes in maintenance requests? Â This data holds valuable insights.
2. Seek Feedback:  Your frontline team – technicians, custodians, and other staff who interact with your facility daily – possess valuable knowledge. Encourage them to share observations and suggestions.  Are there any recurring issues?  Could certain procedures be made more efficient?  Their insights can uncover opportunities for improvement.
3. Embrace Technology Upgrades: The world of facility maintenance software is constantly evolving. Â New features and integrations emerge regularly. Stay informed about these advancements and be open to adopting tools that can further enhance your planning and efficiency.
4. Benchmark Your Performance: Don't exist in isolation. Â Benchmark your maintenance performance against industry standards and best practices. Â Are your maintenance costs in line with similar businesses? Â How does your equipment lifespan compare? Â Benchmarking provides valuable perspective.
5.  Schedule Regular Reviews: Don’t wait for a major problem to arise before reviewing your plan.  Establish a set schedule – quarterly or annually – to review your entire facility maintenance plan with your team. Discuss what’s working, the challenges you’re facing, and potential improvements. Â
By embracing continuous improvement, your facility maintenance planning evolves from a static document into a dynamic tool that drives efficiency, minimizes disruptions, and extends the lifespan of your valuable assets.
Ready to elevate your restaurant's facility maintenance planning? Explore ResQ and discover how its specialized features can simplify your operations and save you money. Learn more about ResQ today!