Customer Stories
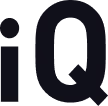
iQ Food increased productivity by 90% using ResQ to scale maintenance management
Key successes
Increase in Productivity
Time Saving
Cost Saving
Company Background
iQ Food Co. has been nourishing Toronto’s downtown workforce through food for over a decade across their nine locations. Arthur Bekerman, Owner and Chief Operating Officer, has leveraged technology to run smooth and efficient back of house and front of house operations from day one.
Arthur is no stranger to working with trade professionals thanks to his background in custom home construction. He’s the kind of hands on operations guru with a rolodex of service providers for each category and knows how to troubleshoot the problem and identify who to call for the job at hand.
Challenge
Scaling Maintenance Operations to Keep Up With Business Growth
Arthur was the go-to for all repair and maintenance issues, so he needed to be on premise or on call for every equipment breakdown or facility-related problem. He’d be the one to source the technician, schedule the service, follow up with staff and trade professionals, and then rinse and repeat the process every single time (often multiple times a day).
Arthur had created the most cost effective mechanism and process for handling repairs and maintenance but with a growing successful business, he needed to also invest his time in growing the business in addition to maintaining efficient operations. Arthur needed to find a solution that would not just match but exceed the cost efficiencies he had already put in place while giving him and his team time back in their day to focus on other areas of the business.
“I pretty much had the role of ResQ at iQ before we joined ResQ’s growing roster of customers. I was excited to hand off end-to-end repair and maintenance work to ResQ knowing they were capable of meeting the high standards of cost efficiency and effective communication we had set at iQ. ResQ has given us 90% of our time back that we would’ve spent on repair and maintenance otherwise.”
“ResQ helped me take back control of my time because I was no longer the de facto equipment expert and tech dispatcher. With ResQ, I had a clear line of sight into our back of house operations across all locations without needing to be on-premise anymore. If you want to take back your life and save time beyond what you can imagine, use ResQ.”
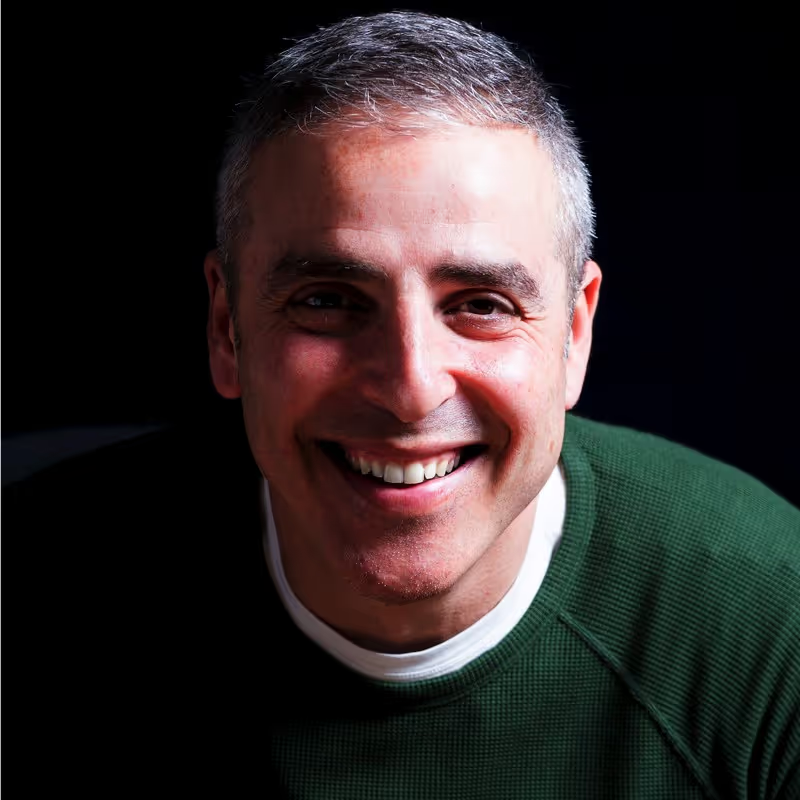
Solution
Taking Repair and Maintenance off iQ’s Plate
ResQ has been part of iQ’s growth story over the past two years by helping Arthur save time so he could focus on growing the business. Arthur and his team have handed off 90% of their equipment repair and maintenance processes and jobs to ResQ. The other 10% of the maintenance work is facilitated using ResQ’s Internal Work Orders to identify, track, approve, and assign jobs to internal staff, further saving the company money and time as a result.
Arthur wasn’t looking for just another technology tool to further optimize his existing repair and maintenance processes. He was looking for a technology partner that could help iQ scale by taking repair and maintenance off their plate and that’s why ResQ has become part of iQ’s operations handbook.
Never lose another dollar to inefficient R&M operations
Connect today to see how ResQ's platform can help you.